Allison transmissions are known for their durability and performance, efficiently transferring power in demanding commercial vehicle applications. However, even the strongest transmissions can experience issues if not properly maintained. One frustrating problem owners may face is fluid leakage from the transmission vent. While alarming, a leaking vent is usually a symptom of an underlying fixable cause rather than a transmission failure. This article will explore the most common reasons for Allison transmission vent leaks and guide troubleshooting and repair.
Overview of Allison transmission vent leaks
The transmission vent, sometimes called the PCV (positive crankcase ventilation) valve or tube, serves the important purpose of maintaining proper fluid levels and regulating temperature. However, when not functioning correctly it can allow fluid to escape, resulting in visible leakage or potential transmission problems over time. This overview will cover the main goals, signs of a leak, and four primary causes mechanics often discover to better understand the issue and its resolution.
What is the transmission vent?
The transmission vent, usually located on the left valve body, regulates fluid pressure and temperature inside the transmission case. As the fluid expands and contracts with rising and falling heat, it needs a path to safely exit the case before the resulting pressure builds to dangerous levels. The vent also draws fresh air to replace exiting fluid vapors. This continuous ventilation is critical for optimum transmission operation and longevity.
Purpose and design of the vent
Most Allison transmission vents employ a weighted diaphragm or flapper valve design. When internal pressure rises from hot fluid, the valve opens to allow a controlled release. As pressure decreases on shifts and during cooldown periods, the valve closes to prevent outside air or fluid from entering. Gaskets and o-rings help create an air-tight seal. Proper vent functioning is essential, as excessive pressure can damage transmission components over time if not safely regulated.
How it regulates transmission temperature
The vent works closely with the transmission fluid cooler and radiator to maintain an ideal operating temperature. As hot fluid passes through the cooler core, heat dissipates into the surrounding airstream. This cooled fluid then returns to the transmission case. Simultaneously, the vent draws warm air out of the case and releases it externally. Repeating this continuous ventilation cycle precisely controls fluid temps within a narrow optimal window.
Signs of a leaking vent
Drivers may first notice signs of a leaking transmission vent through visual leaks or changes in how the vehicle performs. Some common external indications include:
- Fluid staining or puddling near the vent
- Drips visible on the ground after driving
- Fluid residue on nearby components
Internally, a failing vent can also result in issues like:
- Slipping or delayed shifts
- Fluid foaming or overfill errors
- Transmission temperature gauge showing abnormally high or low
- Sudden loss of power or delayed response
So both external visual leaks and transmission performance anomalies should raise concern about the vent’s integrity.
Cause #1 – Pump cavitation
One of the most prevalent causes of Allison transmission vent leaks stems from internal pump cavitation. This occurs when air is introduced into the fluid, usually due to low fluid levels or high fluid temperatures causing vapor bubbles to form. The entrapped air collapses violently each time the high-pressure pump engages, quickly eroding metal surfaces over time.
What is pump cavitation?
Each transmission pump draws fluid in during the intake stroke and pressurizes it to precisely direct hydraulic pressures to shift clutches and brakes. However, if air becomes mixed in instead of pure liquid, it cannot withstand these pressures. The air bubbles implode forcefully within the pump, generating shockwaves akin to small explosions microscopically attacking pump components. Repeated cavitation abrasively wears away at the inner pump housing, seals, and other internals.
How it can cause vent leaks
The destructive erosion from cavitation commonly results in microscopic pump housing pitting and leaks developing over the housing’s outer paper gasket sealing surface. As this seal begins failing, pressurized fluid can find an escape path through the breached seal and out of the vent assembly. Cavitation also regularly damages the valve body and vent seal surfaces, exacerbating any leakage.
Factors that contribute to cavitation
Pump cavitation usually stems from one of two main triggers – low fluid level or high operating temperatures. Low fluid allows air to be ingested into the pump inlet. High fluid temps, on the other hand, cause bubbles to form as the vapor pressure of fluid increases. Both issues need addressing to prevent recurrence.
Diagnosing pump cavitation
While cavitation damage can be difficult to detect visually, mechanics have tests to confirm its existence. They may inspect for pitting inside the pump and on sealing surfaces with a borescope. Fluid analysis can detect microscopic metal particles from erosion. Checking fluid levels and operating temps helps identify probable causes for intervention. Reproducing fluctuating vent seepage only under high loads or high heat further suggests cavitation as the primary culprit.
Common pumps prone to cavitation
Allison transmissions most commonly experiencing cavitation issues tend to be the 1000, 2000, and 3000 Product Families, which use less durable sintered bronze pumps that wear more easily than later alloy steel designs. Older versions also lack modern fluid-level sensors for more precise maintenance. The 1000 RDS pump, for instance, remains a frequent source of vent leaks from cavitation if fluid levels drop too low.
Solution for pump cavitation
To prevent future cavitation, steps should focus on maintaining proper fluid levels and temperatures, along with inspecting for and resolving any issues causing low fluid or overheating conditions. Measures may include:
- Ensuring the dipstick shows a full hot fluid level
- Checking cooler performance and airflow
- Verifying cooler fan operation
- Modifying vent system for extra redundancy
- Upgrading to a more robust pump design if possible
Addressing root causes helps stop the destructive mechanism and safeguard resealed components. If cavitation damage already occurred, pump replacement becomes necessary to fully resolve the vent leakage.
Cause #2 – Overfilled transmission
Overfilling a transmission with too much fluid poses risks like loss of lubrication, aeration, and excessive pressure leading to potential vent leakage. Many mechanics feel 1-2 quarts over the specified hot fill range remains a common misdiagnosed problem source.
Dangers of overfilling
Adding excess fluid beyond capacity essentially overloads the transmission’s ability to safely vent expanding air and gases. The thick fluid acts like a solid when pressurized, providing no easy escape for these expanding byproducts. This forces hot vapors up and out through the vent, seals, and any microscopic leaks.
How excess fluid pushes through the vent
With normal fluid levels, the ventilation system operates as designed – the valve opens briefly to allow pressure release before reseating. But with too much fluid filling all available space, any pocket of air compression has nowhere left to safely displace until encounters a weak point. Constant vent seepage often results.
Checking transmission fluid level
Correctly evaluating fluid levels using the transmission dipstick is imperative. Owners should wait until the transmission and fluid are at normal operating temperature before checking. Gently wiping and fully reinserting the dipstick avoids getting an inaccurate low reading. Fluid should register close to the ‘H’ mark at temperature for proper fill.
Using the dipstick properly
Common mistakes include trying to read an excessively hot dipstick, which causes fluid to run back down before stabilizing. Checking a cold transmission also carries fluid higher on the stick than the real hot fill point. Always follow vehicle specifics and don’t just blindly top it off without verifying the need. Proper evaluation requires a hot dipstick check as a first step before condemning the vent.
Signs the dipstick may be inaccurate
If a fluid level read consistently shows as overfull on accurate hot checks, but the transmission functions fine without vent leaks, the dipstick tube itself may be incorrectly placed too low in the case. A misaligned tube can easily lead to erroneous overfill diagnoses. Mechanics have tricks to validate dipstick placement in suspicious cases.
Solution for overfilling
When overfilling constitutes the cause, the solution requires removing sufficient fluid through the drain plug until properly registers at the hot fill line. It’s critical not to underfill, so the draining process must be slow, safe, and thoroughly checked. Transmission servicing demands care and precision. Afterward, avoid overzealous topping during future fluid changes.
Cause #3 – Overheated fluid
While rarer than the previous two culprits, a transmission overheating issue could potentially contribute to increased venting if allowed to persist. High temperatures change fluid properties in ways that amplify leakage risks through seals and joints.
Potential causes of overheating
- Failures of the transmission oil cooler or radiator
- Low engine coolant levels
- Restricted transmission fluid cooler airflow
- Overly frequent towing/haul-mode use taxing transmission limits
- Loss of transmission fluid causing improper lubrication
Impact on fluid properties
As fluid heat rises past optimal operating ranges, its viscosity or thickness decreases. Thinner fluid has lower sealing abilities. Simultaneously, increased operating temperatures can cause internal vapors to form, expanding under pressure. Together, overheating compromises normal fluid functions and ventilation handling.
Diagnosing overheating
Mechanics check transmission fluid temperatures, inspect cooling system components, review maintenance histories for causal clues, and may road test under heavy load conditions to attempt to reproduce overheating issues. Verifying components function as designed helps identify compromised parts. Transmission temperature sensors and diagnostic trouble codes also assist in evaluating overheating problems.
Clue transmission is overheating
- Abnormally high operating temperature readings
- Transmission shifting harshly or sluggish upshifts
- A burning or distinct transmission fluid smell noticed
- Drivability anomalies alleviated with slowed acceleration
- Recent fluid discoloration from overheating breakdown
Ruled-out other potential causes
It’s important mechanics thoroughly eliminate the two previous root causes of low fluid level or overfilling before implicating overheating. A failing transmission cooler could exacerbate venting from other underlying reasons rather than serve as the standalone problem source. Comprehensive testing examines all probable factors.
Solutions for overheating
To correct overheating contributing to venting, technicians focus repairs on malfunctioning cooling system parts like bad coolers, clogged radiators, or failing transmission fluid temperature sensors. Software updates may help if control module issues exist. Maintenance schedules also assess excessive workloads and overwhelming transmission capacity to prevent recurrence.
Cause #4 – Disassembled vent
In rare cases, a vent assembly may become disassembled through owner tampering, accident damage detaching components, or as a byproduct of previous repair attempts. Loss of proper vent sealing then allows internal pressures to force fluid releases.
Impact of seal or gasket issues
Much like overfilling situations, a disassembled or broken vent increases risks of internal air and vapors unable to safely vent before pressure builds up. Seals, gaskets, or o-rings no longer form an airtight barrier, so microscopic leaks inevitably form pathways for fluid to escape under rising pressures.
Inspecting the vent assembly
To examine this possibility, mechanics completely disassemble, clean, and visually inspect all vent housing components for signs of external impact or dislodgement. They especially evaluate the integrity of sealing surfaces and check o-rings or gaskets for cracks, compression, or slippage from their intended positions. Even microscopic seal defects provide openings.
Closely examining vent components
Borescopes allow technicians to internally inspect areas normally not viewable, searching for telltale damage. Lube depositories also undergo scrutiny under bright lighting. Seams receive non-destructive testing to detect hairline fractures. Meticulous vent dissection uncovers any assembly, fit, or finish issues potentially necessitating repair or replacement parts.
Checking for signs of tampering
If evidence surfaces suggesting prior vent alteration instead of manufacturing or incident-related problems, shops question owners about warranty status implications. Tampering risks voiding coverage if part of the issue’s original root cause. Technicians document all findings to support diagnosis and repair recommendations.
Solution for disassembled vent
When inspections reveal a detached, loose, or damaged vent assembly allowing improper ventilation, mechanics must correctly reassemble components as designed while addressing any unsealed areas. New seals, gaskets, and o-rings replace compromised parts to perfectly perform leakproof vent sealing. In severe cases, total vent replacement becomes necessary.
Preventing future leaks
Fortunately, diligent fluid maintenance and monitoring transmission operating parameters help safeguard against many vent leak triggers down the road. Consistent care delivers years of problem-free use. Transmission specialists understand nuanced vehicle applications and can create customized preventive plans.
Regular fluid maintenance schedule
Allison recommends checking and changing transmission fluid and filters based on operating hours or yearly, along with coolant services. This flushes contaminants and restores inhibited formula protecting metal surfaces. Early fluid degradation catches problems before escalating. Adhering to OEM change intervals proves crucial for long life.
Monitoring for underlying technical issues
Checking transmission fluid levels and temperatures also identifies potential issues before escalating. Immediate repairs prevent aggravating downstream concerns. Carefully evaluating any new drivability issues, noises or warning lights helps mechanics spot trends warranting attention. Periodic system inspections spot troubles early.
Other signs of transmission problems
Watching for other anomalies besides vent leaks assists with quickly addressing underlying issues before culminating in component damage or costly repairs down the road. Symptoms like slipping or delayed shifts, sudden power loss, transmission fluid leaks, or unusual noises signal the need for closer examination. Ignoring subtle signs risks compounding.
Relationship to potential vent leaks
Many symptoms requiring service might not directly relate to vent leaks but represent precursors if left unresolved. Their timely repair helps ensure long-term vent and transmission integrity by removing conditions that increase seal and component wear risks over time, like overfilling, low levels, cavitation, or overheating previously discussed. Comprehensive assessments gauge full system health.
When to call a professional
While minor fluid changes remain DIY-friendly for some, complex issues like diagnosing root causes, checking transmission parameters, or disassembling internal components demand experienced professional help. Signs warranting a transmission specialist include:
- Multiple drivability problems emerge together
- Inability to properly diagnose the specific failure source
- Symptoms persisting after attempted fixes
- Visible leaks spilling large volumes of fluid
- Harsh shifting or loss of gears occurring
- Fluid contamination, burning smells, or dark coloration
- Suspected electrical or computer-related issues
Amateurs risk costly mistakes on sophisticated drivetrains. Certified transmission technicians leverage specialized tools, training, and certifications for correct repairs.
Serious issues beyond DIY repair
Transmission failures pose safety risks if ignored, endangering drivability when problems accelerate unattended. While minor jobs might attract DIY savings, complex multi-issue concerns require professional-grade diagnostic equipment, technical service information access, and broad expertise. Misdiagnosed transmission problems frequently damage more components before repair. Specialized shops properly assess all systems to completely resolve customer issues.
Benefits of a transmission specialist
Beyond possessing factory service manuals proprietary to dealer technicians, certified all-makes transmission experts receive extensive technician training on the inner workings of varied automatic drivetrains. Their diagnostic prowess recognizes subtle trends from years of hands-on experience. Customers gain peace of mind knowing that highly skilled professionals thoroughly inspect, diagnose, and fix transmissions correctly with high-quality lifetime parts.
Vent leak overview
Reviewing the most common vent leak causes helps mechanics systematically troubleshoot transmission problems:
- Pump cavitation due to low fluid levels or overheating physically deteriorates component seals over time.
- Overfilling transmissions force vapor pressures up and out any microscopic port of least resistance like the vent.
- Sustained high operating temperatures change fluid properties compromising normal ventilation handling abilities.
- Disassembled or damaged vent assemblies disrupt designed air-tight barrier functions.
Most common reasons
While all causes remain possible, pump cavitation and overfilling represent the two most prevalent triggers necessitating repairs according to industry surveys. Consistently maintaining proper fluid operating parameters through quality-minded care prevents 95% of issues. Correctly diagnosing root problems fixes vent leakage for the long haul.
Additional troubleshooting tips
Besides systematically addressing each known cause, extra checks help mechanics thoroughly diagnose complex concerns:
- Examining removed trans vent components under magnification for microscopic clues
- Performing fluid analyses detecting wear particles from cavitation or contamination
- Temporarily rerouting vent lines to fluid reservoirs and observing behavior changes
- Taking fluid level, temperature, and system pressure measurements under varying loads
- Placing transmission on a lift accessing hidden areas for better inspections
- Utilizing specialized leak-down and pressure tests on seals and components
Helpful checks before attempting repairs
Before disassembling or removing transmission parts, mechanics closely:
- Inspect all external vent areas, tubes, hoses, and clamps for signs of leakage
- Verify dipstick shows proper hot fluid level
- Check fluid coloration and smell for burnt odors
- Review maintenance records and repair histories for new insights
- Road test if possible with monitoring parameters under different loads
This thorough pre-repair evaluation helps isolate root causes rather than chasing secondary effects.
When to suspect transmission rebuild
While vent issues may prove fixable through isolated gasket or seal replacements, owners should anticipate potential rebuilds for high-mileage Allisons or those experiencing chronic multiple problems from deferred maintenance. The following signs frequently warrant transmission overhauls:
- Severe leakage necessitating frequent fluid top-offs
- Slipping, delayed, or erratic shifts across the board
- Complete loss of any individual gears
- Suspected worn clutch plate friction materials
- Prior history neglected fluid/filter services
- Known problematic applications like police cruisers
- Transmissions surpassing 250,000-300,000 miles
Rebuilds restore specifications and predictability.
Special considerations for 2001-2004 models
Allison 1000 and 2000 Product Family transmissions manufactured between 2001-2004 carry extra attention for their vulnerable pumps known to prematurely fail and leak. These units typically require remanufactured pumps around 250,000 miles as a preventative measure due to design limitations. Owners would be wise to budget for this common upgrade.
Known pump issues for those years
Allison addressed the weak sintered bronze pump design in newer models with more robust and longer-lasting alloy steel replacements less prone to cavitation damage. However, 2001-2004 examples remain at risk and should factor in the likely eventual OEM pump replacement during scheduled service intervals to avoid potential downstream expenses from pump failures. Periodic fluid analyses help detect pump wear beforehand and properly time repairs.
Extended maintenance recommendations
Beyond following recommended service intervals, higher mileage commercial Allisons or applications facing tougher duty cycles necessitate stepped-up fluid maintenance, including:
- Changes every 30,000 miles or annual intervals for light-medium duty use
- 20,000-mile intervals for heavy-haul trucks or rugged terrain operations
- Periodic fluid sampling detects contaminants before harming components
- Transmission flushes sustain additive packages over long operating periods
- Increased cooler services address higher heat loads from workloads
- More frequent filter replacements catch higher wear particulate volumes
Consistent care preserves transmissions working in severe environments.
External vent tube modification
As an optional upgrade for applications constantly venting fluid, mechanics install auxiliary vent tubes directing any excessive pressure releases safely away from vulnerable seals and components prone to leaks. Bypass routes relieve pressures through fluid accumulators before reaching vent areas. This low-cost modification provides an extra layer of protection against vent leakage recurrence.
Benefits of this optional upgrade
Vent tube rerouting offers insulation for the sensitive diaphragm valve areas by diverting persistent high pressures away from seals. It also helps diagnose issues by monitoring accumulator fluid levels for visible leaks rather than relying on only intermittent externally visible drips. As a proactive measure, rerouted venting protects seals during troubleshooting periods and acts as a redundancy against future problems.
Final checklist before repairs
Before attempting transmission work, a complete pre-repair evaluation ensures no overlooked factors:
- Transmission at operating temperature for level/inspection
- All fluid leaks stopped and sources found
- Proper fluid level via the accurate dipstick
- Fluid quality/color/smell inspected
- Cooling systems functioning correctly
- Pressures/temps within parameters
- Drivability concerns duplicated/resolved
- Inspections locate the root cause
- Parts/tools/manuals prepared
- Safety equipment/lifts inspected
- Drain pans/rags/funnels ready
Thorough preparation sets the stage for successful repairs.
Fluid draining and filling process
Draining Transmission Fluid:
- Remove fill plug
- Place the drain pan under the transmission pan
- Remove pan bolts and drain fluid
- Inspect old fluid for metal, contamination
- Reinstall the pan and new gasket
Filling Transmission:
- Clean the dipstick and replace it in the tube
- Fill through fill tube slowly until at the hotline
- Inspect for leaks during fluid expansion
- Reinstall fill plug
- Allow time to circulate before the test drive
Tips: Go slow to avoid aeration. Use OEM-specified fluid only.
Critical do’s and don’ts
General fluid-changing guidelines help prevent problems:
Do:
- Drain fluid when the transmission is hot for accurate volume
- Use the correct Allison-specified fluid for your model
- Tighten pan bolts evenly in stages with proper torque
- Allow time for fluid circuiting before test drives
Don’t:
- Overfill past hotline after draining
- Mix different fluid types without a flush
- Leave bolts loose or overtighten risking leaks
- Immediately run if the introduction of air pockets exist
Careful habits yield optimal fluid film protection and maximum component life.
Disassembling the vent assembly
- Loosen vent housing bolts in a crisscross pattern.
- Carefully separate the vent housing from the valve body.
- Inspect gasket sealing surfaces for irregularities.
- Remove the diaphragm/flapper and o-rings from the housing.
- Thoroughly clean all parts in solvent.
- Examine o-rings for cracking or compression set damage.
- Inspect the valve area bore for signs of cavitation.
- Check the diaphragm for puckering, splits, or material degradation.
- Replace all worn components with new OEM quality parts.
Proper disassembly and cleaning aid accurate diagnosis.
Replacing vent gaskets and seals
Gaskets must form an even compression seal:
- Lubricate new o-rings lightly for easy insertion.
- Install valve from inside housing bore first.
- Press o-rings fully into grooves without pinching.
- Apply sealant to gasket mating surfaces evenly.
- Align vent housing during assembly for bolt holes.
- Gradually tighten bolts in a crisscross pattern to spec.
Correct sealing ensures no vented pressure bypass.
Reattaching the vent
Reattaching the vent housing requires care:
- Inspect housing bolt holes for damage or elongating.
- Lubricate bolt threads to avoid stripping.
- Position gasket and housing with bolt holes aligned.
- Start bolts by hand before using a torque wrench.
- Tighten bolts evenly in a crossing pattern to spec.
- Recheck torque after 30 minutes to catch any loosened bolts.
Proper torquing compresses the gasket for a leakproof seal.
Final inspections and tests
Before returning the vehicle to service:
- Inspect for leaks with the engine running for 15 minutes.
- Check fluid level and top off slightly if needed.
- Perform test drives with transmission temp gauge.
- Verify no new issues emerge under varying loads.
- Road test transmission parameters for smooth shifts.
- Respond quickly if original concerns resurface.
Thorough post-repair validation finds any missed issues.
Drive cycle to check repairs
To fully assess transmission repairs, test the following drive cycle:
- Accelerate from a stop sign up to 45 mph
- Maintain 45 mph for 10 minutes
- Slow down and idle for 5 minutes
- Accelerate from idle to the posted speed limit
- Drive at varying highway speeds for 30 minutes
- Exit highway and brake to 30 mph
- Idle in a drive for another 5 minutes
- Park and let transmission fully cool
Observe fluid levels, noises, slipping, and how it shifts through all gears under varying loads and speeds before fully approving repairs.
What to do if the issue persists
If symptoms reoccur after diagnosis and repairs, carefully reconsider:
- Overlooked conditions bypassing original fixes
- Inaccurate diagnoses leading repairs astray
- Worn components requiring early replacement
- Improper repair techniques compromise work
- Relevant technical service bulletins for issues
Thorough re-evaluation guides correcting any missed work to finally solve persistent problems.
Common FAQs
Q: How often should I change my transmission fluid?
A: Allison recommends every 30,000 miles or yearly for most applications. Severe service may require more frequent fluid/filter services. Use OEM-specified fluid only.
Q: What are the signs of transmission failure?
A: Shifting problems, fluid leaks, slipping, loss of gears, or sudden loss of power signal need for inspection. Ignoring issues risks expensive repairs.
Q: How much does a transmission rebuild typically cost?
A: Shop labor rates vary, but ballpark costs are $3,000-5,000 for most remanufactured Allison rebuilds depending on your model and extras needed.
Q: What causes sudden transmission failure?
A: Neglected maintenance allowing contamination, overheating or worn components to progress can unexpectedly cause transmission seizures. Consistent care helps prevent catastrophic failures.
Q: When should I consider a used transmission instead of a rebuild?
A: For high mileage applications over 250,000 miles or if damage from deferred maintenance would be too extensive, a lower mileage remanufactured unit may provide the best value over a full internal transmission rebuild.
Additional troubleshooting questions
Some other issues mechanics probe include:
- Are any aftermarket parts or modifications potentially impacting performance?
- Prior transmission accident damage or repairs completed?
- Towing or hauling extremely heavy loads frequently?
- Transmission ever submerged or exposed to moisture?
- Consistency of shifting profiles change over time?
- Are shops previously inspecting transmission found anything?
- Fluid turned dark brown or burnt fluid smell?
- Engine or transmission codes stored in the computer?
- Customers report any other vehicle issues recently.
Thorough questioning aids in accurate diagnoses.
Preventing recurrence
Proper long-term transmission care prevents many issues:
- Change fluid/filter regularly as recommended
- Inspect transmission coolers and airflow annually
- Check fluid levels when hot at each oil change
- Watch for leaks and fix causes – don’t ignore them
- Use approved Allison ServiceFill fluid only
- Monitor for codes/symptoms and fix problems promptly
- Tow carefully within transmission temperature limits
- Follow usage guides for applications/ vocations
- Obtain transmission rebuilds before extensive wear
Conscientious maintenance sustains optimum performance.
Routine maintenance practices
Key steps to protect Allison transmissions:
- Change fluid/filter every 30k miles or annually
- Inspect transmission coolers yearly for blockages
- Check fluid color every oil change for burnt odors
- Tighten cooler lines clamps regularly
- Replace faulty transmission temperature sensors
- Maintain engine cooling system properly
- Use only Allison-recommended ATF fluid
- Tow within transmission temperature parameters
- Repair leaks and fix problems immediately
- Maintain according to harder-duty service intervals
Consistent habits safeguard service realities.
Sign-up for transmission rebuild reminder
Allison transmissions generally last 250,000-300,000 miles with proper fluid services. However many commercial fleets exceed 20,000 annual miles. As a proactive measure, fleet managers should sign up for a transmission condition monitoring program alerting them at 200,000 miles to budget for upcoming transmission rebuilds every 3-5 years based on the duty cycle. Catching rebuilds preemptively avoids downtime.
Typical shop labor rates
Independent transmission specialists may charge:
Diagnosis: $100-150 per hour
Remanufactured Rebuild: $2,500-5,000
Used Transmission Install: $1,000-2,000
Fluid/Filter Service: $250-500
Vent Assembly Repair: $300-600
Pump Replacement: $1,000-1,500
Electrical Diagnosis: $150-200 per hour
Rates vary by shop but provide a general cost idea for transmission repairs. Certified technicians using lifetime warranty parts offer the best value.
Expectations for vent fix vs full rebuild
A vent leak repair targeting the root cause usually solves the immediate problem for $300-600 including diagnosis if only filter/gasket work is needed. However ongoing issues hinting at other wear may lead to predicting a future rebuild. Rebuilds averaging $3000-5000 restore optimal performance and provide 100,000-mile warranty coverage preventing recurring concerns and offering long-term reliability. Weigh repair vs rebuild carefully based on application and history.
Manufacturer coverage details
Allison transmission factory warranties potentially cover defects for the first 2 years/unlimited miles. Component warranties span 5 years or 100,000 miles on specific modules. Abusing or neglecting maintenance and adhering strictly to intervals usually voids the warranty. Check specific vehicles and applications for any extended coverage which may add 1-2 years if serviced by authorized facilities. warranties promote long-term dependability.
Owner testimonials
“After struggling with a vent leak for months, the transmission specialists finally properly diagnosed it as pump cavitation caused by low fluid levels. The new pump fixed it for good along with resetting fluid change intervals to prevent a recurrence.”
- Mike T., Fleet Manager
“Both vent leak attempts by other shops failed until we came to XYZ Transmissions. They thoroughly inspected everything, found overfilling causing issues, and repaired it right with no recurrence in 50k miles since. I recommend them highly for their expertise and honesty.”
- Carol B., Independent Operator
“Our Allison in the bucket truck leaked multiple times until changing shops. They discovered a failing transmission cooler and fixed the root problem instead of just the symptom. Transmission has been solid ever since with their preventative maintenance plan.”
- Roger C., Utility Lineman
Positive outcomes inspire confidence in transmission specialists focused on thorough fixes addressing underlying causes rather than chasing repeated symptoms. Finding the right pro upfront saves money and downtime long-term.
Allison transmission overview
Allison transmissions are automatic transaxle assemblies used primarily in medium and heavy-duty commercial vehicle applications like trucks, buses, and military vehicles. They feature:
- Fully automatic or semi-automatic electronically-controlled operation
- Hydraulically-actuated wet clutch multiple disc design
- Models include the 1000, 2000, and 3000 series holding various gear ratios
- Capable of handling high-torque diesel engines up to 550 lb-ft
- Precisely calibrated shift points matching engine/load requirements
- Integrated transmission mounts for vehicle interfaces
- Fluid cooled with transmission oil cooler circulation
- Electronic controls networked through vehicle data
Their durability and efficiency prove why Allison remains an industry-leading commercial transmission supplier.
Known technical issues to watch out for
While generally very robust, certain Allison models may present increased risks of some issues based on variants, applications, or periods:
- 2001-2004: 1000/2000 series susceptible to premature pump failures
- High idle hours: Increased wear necessitates more frequent rebuilds
- Towing/haul applications: Repeated high loads shorten component life
- H-Series: Friction material or clutch cylinder concerns on older versions
- Extended idling: Contributes to fluid degradation needing faster changes
- Off-road use: Severe conditions exacerbate wear and require stepped-up maintenance
Understanding applications and potential weak points owners and fleets to proactively address trouble areas during preventative maintenance.
Transmission fluid types explained
Allison transmissions strictly require approved fluids meeting set specifications:
- Type T – Conventional Non-Synthetic ATF for older transmissions
- Type F – Friction Modified Non-Synthetic for improved shift feel
- Type TD – Dexron IIIH or Mercon-compatible synthetic ATF
- Type TE-2 – API GL-4 Synthetic low-viscosity fluid for new designs
- Type TES 389 – Temp synthetic for diverse operating conditions
Fluid selection matches transmission, usage, and temperature ranges. Only approved Allison fluids ensure optimum protection and shift performance. Never mix fluid types without a flush.
Glossary of transmission terms
Automatic Transmission: Uses a hydraulic/electronic control system to perform gear changes automatically.
Clutch: Friction plates that engage/disengage to change transmission gears.
Component: Individual part that makes up the transmission such as gears, shafts, and pumps.
Fluid: Transmission fluid is a specially formulated hydraulic fluid circulating internally.
Gear Ratios: Speed and torque multiplication ratios within the transmission.
Valve Body: Controls transmission fluid flow directing hydraulic pressures to clutches.
TORQUE CONVERTER: A fluid coupling device between the engine and transmission.
PCM: Powertrain Control Module electronically controlling ignition, fuel injection, and transmission.
Bands: Fricition material acts like a clutch connecting transmission gears instead of clutch packs.
Filters: Screen particulate contamination from transmission fluid flow.
Understanding key terminology assists communication between technicians and customers.
Real-world cost analysis
Owning an Allison transmission long-term breaks down financially:
- Purchase Price: $3,000-6,000 remanufactured depending on model
- Fluid/Filter Service: $250-500 every 30k miles or annually
- Cooler Service: $150-300 with each fluid change as needed
- Vent Assembly Repair: $300-600 if ever required
- Rebuild/Overhaul: $3,000-5,000 every 250k-300k miles
- Diagnosis/Inspection: $100-150 hourly rate as needed
- Extended Coverage: Additional $1,000-2,000 for upgrades
Proper ongoing maintenance costs about $1,000-1,500 annually but prevents far greater repair bills down the road from neglected upkeep. Timely care equals big savings versus deferred maintenance consequences. The transmission remains one of the most important and valuable components of any commercial vehicle.
When a second opinion helps
Any time transmission concerns persist after repairs or for hard-to-diagnose issues, a second expert evaluation offers peace of mind:
- If drivability anomalies continue unchanged
- When multiple symptoms surface together complexly
- Prior diagnosis and repairs failed to fully address problems
- Transmission history reveals complex repair pattern
- Important applications can’t afford missed repairs
- Desire to verify repairs before the costly warranty period ends
A fresh set of eyes may catch subtle clues missed initially to finally resolve stubborn problems. In complex cases, a second pro assessment provides reassurance that repairing the transmission correct.
Preventing transmission rebuild scams
As critical components, transmissions attract dishonest shops preying on unsuspecting customers. Watch for these red flags:
- Shops without certifications, online reviews, or proven experience
- Vague diagnostic processes justifying excessive repair scopes
- Overstating normal wear patterns as “failures” necessitating rebuilds
- Never produce failed parts for customer examination
- Recommend unwarranted rebuilds under factory warranties
- Push customers for rushed decisions without options
- Provide no test drives, trials, or second opinions on repairs
- Perform rebuilds without proper fluid/filter services first
Deal only with reputable licensed professionals standing by the workmanship and verifiable transmission repair expertise. Prevent undue financial losses from unscrupulous practices.
Structure:
Tables
Maintenance Schedule Based on Application
Application | Fluid Change Interval | Filter Change Interval |
---|---|---|
Light Duty (under 10k miles/year) | 30k miles or 1 year | 60k miles |
Medium Duty (10k-20k miles/year) | 20k miles or 1 year | 40k miles |
Heavy Duty (over 20k miles/year) | 10k miles or 6 months | 20k miles |
Severe Service/Tow Trucks | 5k miles or 3 months | 10k miles |
Common Transmission Fluid Types
Fluid Type | Description | Applications |
---|---|---|
T | Conventional ATF | Pre-1999 Allison transmissions |
F | Friction Modified ATF | Improved shift feel in older transmissions |
TD | Dexron III/Mercon Compatible Synthetic | Most light-medium duty Allisons since 1999 |
TE |
Signs of Transmission Failure
- Fluid leaks
- Slipping or rough shifts
- Delayed or lack of shifts
- Loss of power
- Burning smell from fluid
- Transmission making new noises
Steps for Safe Fluid Draining
- Warm-up transmission to operating temperature
- Position the drain pan securely beneath the transmission
- Remove the drain plug slowly to avoid fluid splashing
- Inspect old fluid for signs of wear or contamination
- Replace the pan gasket if the old one is worn or damaged
- Reinstall the drain plug securely when finished
Tips for Accurate Fluid Filling
- Use the correct specification fluid for your transmission
- Remove the filler plug before adding fluid
- Add fluid slowly through filling the hole
- Check fluid level regularly as you fill
- Do not overfill past the maximum level
- Inspect for leaks after filling is complete
- Retighten filler plug securely
Statistics
- The average lifespan of an automatic transmission with proper maintenance is 150,000-200,000 miles.
- Failure to change transmission fluid as recommended cuts expected service life by 50%.
- Overfilling transmission fluid is a factor in 20% of transmission repair cases.
- The top three transmission problems are worn bands/clutches, low/contaminated fluid, and valve body issues.
- Transmission repairs account for nearly 20% of overall repair bills for older vehicles.
- Prompt fluid changes every 30,000 miles pay for itself by extending transmission life 2-3 times versus neglecting maintenance.
Related posts:
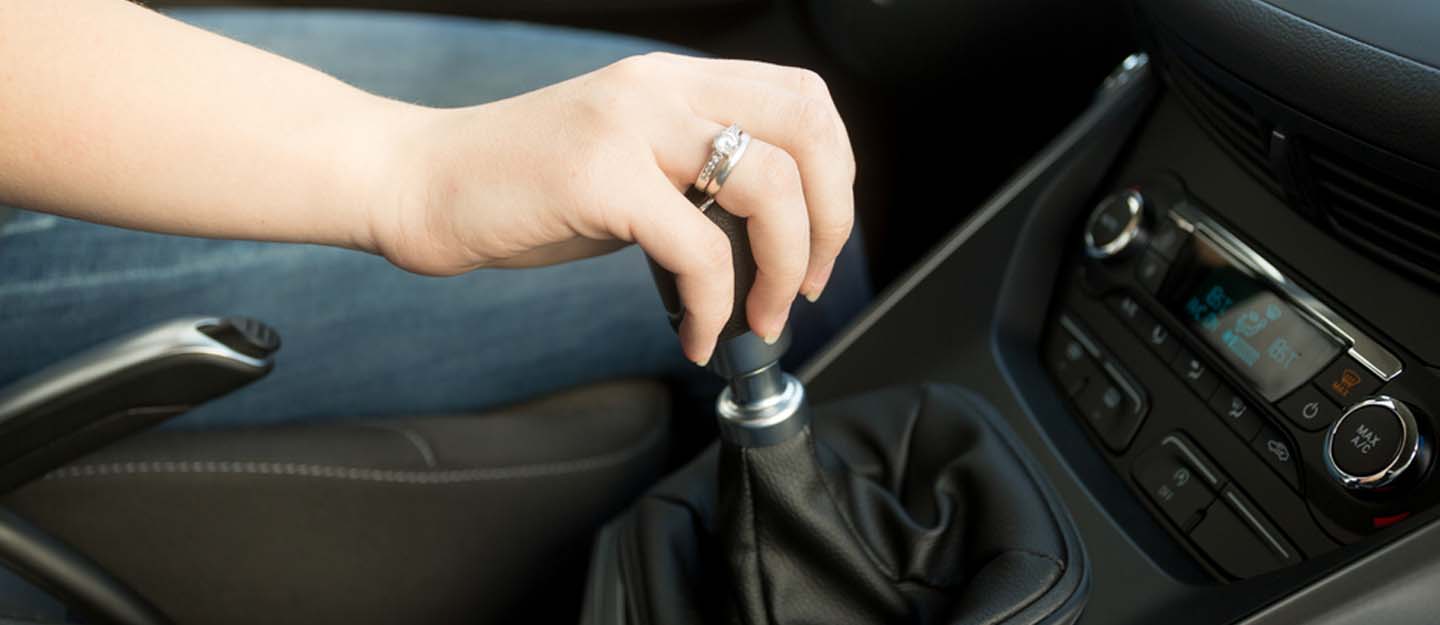


















